专用夹具设计时的注意事项与案例分析
引言:在加工应用中,想要利用好一些自动化设备会需要设计一个合适的专用夹具,以最大限度地发挥加工设备的性能。在实践中摸索和总结了一些加工设备专用夹具设计的经验与大家分享。
工件的定位基准要保证基准统一的要求,即工件经多次装夹后,为保证其加工表面之间相互位置的正确性,应采用统一基准定位,可避免因基准转换而引起的误差,同时又要满足加工中工序集中的特点,即工件在一次安装中尽可能完成较多的加工表面。
工件定位基准的合理与否,将直接影响工件的加工品质与生产效率,在选择定位基准时,应根据加工设备的工艺特点,全面考虑各部位的加工要求,尤其应关注以下要点。
专用夹具设计注意事项
设计夹具的夹紧机构时,应保证夹具有足够的刚度和稳定性,尽可能提高工件的装夹刚性,减少加工过程中的振动。不合理的装夹也会造成工件变形,影响加工精度。
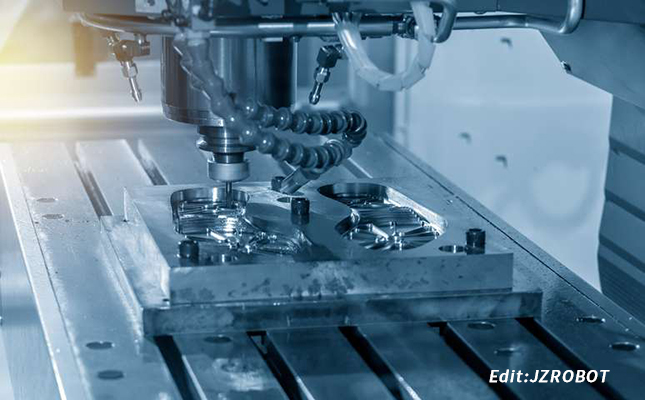
1、夹具必须保证工件最小变形。粗加工时,切削力大,则夹紧力大,但不能使工件发生夹压变形。
2、夹紧机构元件与工件加工面之间应保持一定的安全距离,同时要求夹紧机构简单、可靠,以免加工过程中发生任何干涉或碰撞现象。
3、尽是减少工件装夹次数,尽可能在1次定位装夹后完成所有的待加工表面。对于一些箱体类零件,尽量采用1面2销的定位方式,以便加工较多的表面。
4、在考虑夹紧方案时,夹紧力应在主支承点上,力求靠近切削部位及刚性好的部位,避免夹紧点选在被加工孔的上方。因此,夹紧力的方向应尽量与切削力、工件重力等方向保持一致,以减少夹紧力,且垂直指向工件刚度最大的方向,以防止或减少工件变形。
5、对于加工精度要求高的工件,可采取粗、精加工分开的方式(或者粗、精加工使用大小不同的夹紧力),或者在粗加工后编一任选停止指令,操作者松开压板,待工件消除变形后重新夹紧再进行精加工,以保证精度要求。
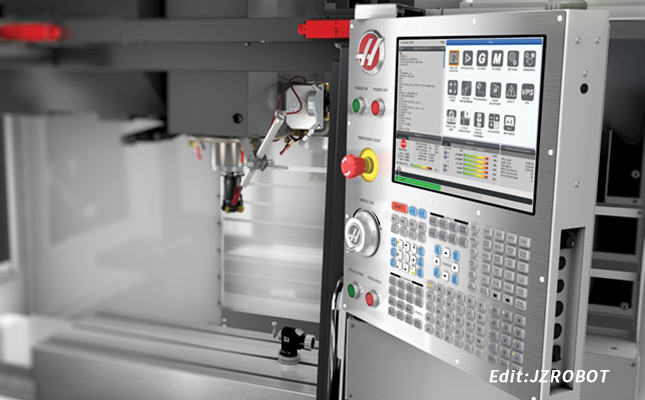
专用夹具设计案例分析
在数控加工过程中,并非所有零件都适合直接数控加工,比如圆柱形坯料就需要辅以专用夹具才可实现精细加工。数控加工工艺具有自动化程度高、加工精度高、能加工复杂型面、零件一致性好、生产效率高等优点,但同时其生产成本高、维修存在局限性,而且加工中难以调整,这就需要借助专用夹具的辅助作用来提升加工工艺水平。
在分析并设计工件数控加工专用夹具之后,需要通过实体加工来验证专用夹具的性能和效果。根据数控加工工艺的不同,验证平台的选择也会有差异,本文介绍的专用夹具需通过基于MasterCAM软件为平台验证应用结果。
在验证工件数控加工专用夹具的实际应用中,需要进行数控编程。对实体进行分析,利用ProENC编程,建立自己的加工模型。与普通机床夹具相比,数控机床上的专用夹具除了要给1个基准面以外,还要求提供1个回转中心。
通过文中介绍,我们知道了专用夹具设计时的注意事项,包括需要控制夹具的夹紧力,不能使工件发生夹压变形。同时通过案例分析,了解了与普通机床夹具相比,数控机床专用夹具需要的配置。更多关于专用夹具的知识和应用,请关注我们吧。