数控车床设计自动上下料气动机械手实现棒料输送
引言:本文主要介绍的数控车床设计,其中以设计一款自动上下料气动机械手为例,能够实现全自动棒料输送与更换。设计内容包括:研制目标与技术路线、上下料系统的结构、卸零件系统的结构、上下料系统的控制等。
数控车床能够车削轴类零件或盘类零件的内外圆柱面、任意锥角的内外圆锥面、复杂回转内外曲面和圆柱、圆锥螺纹等,广泛应用在所有机械加工的任何领域,更是模具加工的发展趋势和重要和必要的技术手段。
一、研制目标与技术路线
随着机械制造工业的发展,我国用步进电机驱动的经济数控车床日益增多,为了适应多品种小批量生产及提高生产力的要求,用户希望提供轴类零件上下料系统,能够输送15~25mm的棒料,并能卸下尺寸不等的轴类及片状零件,价格应低于车床价的四分之一。
从用户的要求来说,显然上下料系统应有柔性。传统的凸轮连杆、开关型气缸等难以独立实现,示教再现型机器人也难以完成将尺寸不等的轴类及片状零件卸入零件箱的任务。我们借助机电一体化思想,寻找机与电为一体的结合点,用电子信息使刚性的气缸、凸轮、连杆等实现柔性要求,发生质的飞跃,形成具有柔性的上下料系统,获得很好的功能价格比。
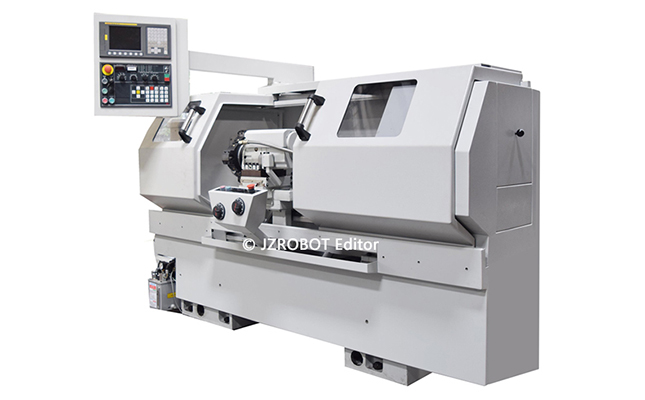
二、上下料系统的结构
气缸驱动具有结构简单、价格低廉、使用及维护容易等优点。但是气体压缩性大,普通开关控制难使活塞停在任意位置。因此,它不能按任意零件尺寸送进相应长度的棒料,但当活塞顶靠气缸盖(相当机械档块)时,重复定位精度高达0.03mm。我们利用数控车床的刀架作机械档块,气动机械手在0.2~0.3MPa的气压推动下,使棒料穿过车床主轴孔及卡盘孔顶到刀架及开关上,刀架位置由车床数控系统按需要加工零件的尺寸控制,从而实现送料柔性,送料精度达到0.03mm,能节约材料及加工费用。
气动机械手的活塞杆顶端安装了径向轴承及端面轴承,起支承限位作用,棒料在其中旋转时只能带动轴承内圈旋转,不会引起活塞杆旋转。
为防止车削长棒料时可能产生大幅度振动,在车床头部安一个气动中心架,3个气缸受同一个气阀控制,进气时3个活塞杆顶部的橡皮滚轮同时压紧棒料,并随棒料转动而自转,使棒料处于车床主轴中心位置,从而防止或减少振动。活塞杆伸入车床主轴孔送料时,橡皮滚轮可压在活塞杆上,起支承作用。当棒料被加工到剩下卡头时,机床的控制系统使刀架后退,残料落入废料箱中,同时使机械手退回原位,将下一根棒料送上,连续给机床供料。每次送料长度随需要加工零件的尺寸而变,实现上料柔性自动化的要求。
当用户在原来的数控车床生产场地上进行技术改造,能用于安装上料系统的场地小时,可采用多级气缸或普通气缸组合成的廉价上料系统,以缩短上料系统的长度。
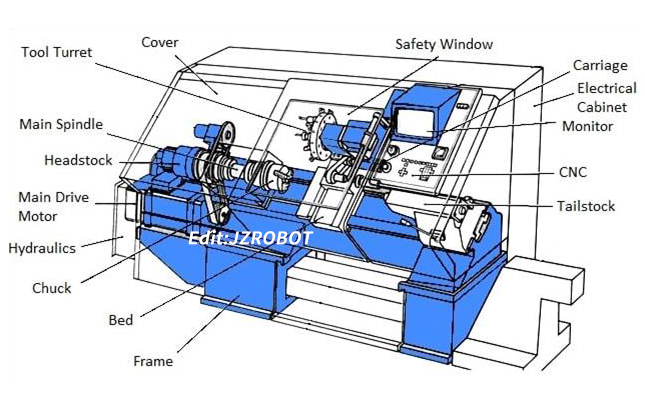
三、卸零件系统的结构
由于零件的直径在10~25mm之间变化,长度变化范围更大。车刀将零件从棒料上切下的瞬间,工业机器人不能抓取零件,具有手眼协调系统的智能机器人也难快速跟踪抓取零件。我们首先考虑将机械手放在数控机床刀架的大拖板上,以解决跟踪车刀切下零件的位置变化问题,再改变手指抓零件的思路,采用机械手模拟人手从下面接切断后落下的零件,以适应零件直径及长度尺寸的变化。为简化结构,降低费用,借用车刀切断零件时的联动,在中拖板上安装一个滚轮,当加工完零件表面,在车刀切断零件的过程中,中拖板上的滚轮前进,逐渐使大拖板上的卸件机械手旋转到零件之下,零件切断时刚好落入其中,车刀退回原位时机械手在弹簧作用下转回原位,将零件卸入零件箱中。
四、上下料系统的控制
上下料系统包含隔料器放出一根棒料、气动机械手向前送进棒料及退回原位时,都用电磁铁实现简单的开关控制。机械手送料与车床卡盘张开、卡紧及车刀运动有联锁关系,其程序如下:车床启动——卡盘张开——刀架按输入数控系统的加工零件尺寸运动到初始位置——隔料器放出一根棒料——机械手向前送进棒料——开关发出棒料到位信号——车床卡盘夹紧棒料——加工零件——车刀切下零件——刀架按输入数控系统的加工零件尺寸运动到初始位置——卡盘张开——机械手向前送进棒料——开关发出棒料到位信号——车床卡盘夹紧棒料——按上述程序循环加工,一根棒料被加工完毕后——控制系统发出信号——机械手退回原来位置——隔料器放出下一根棒料——机械手再向前送棒料——循环。卸零件机械手由大拖板及中拖板带动,不需将工作单独编入控制系统。
五、总结
1、普通气缸驱动的机械手借用数控车床的刀架,相辅相成,可实现柔性自动送料,送料精度0.03mm,能节约材料及加工费用。
2、引用了经典的凸轮连杆机构运动原理,借刀架大拖板及中拖板的联动研制成功卸零件机械手具有很好的柔性,能可靠地将直径及长度不同的零件卸入零件箱中。卸零件时间与车刀切断零件时间重叠,不但省事、减少投资、节约时间,而且可靠性很好。
3、上下料系统的结构简洁,高性价比,具有很高的功能性及实用价值。